1. INTRODUCCION
Las coronas de las masas superior, cañera y bagacera de los Molinos del Tandem de Molinos de los Ingenios Azucareros son mecanismos que transmiten altos torques en Nm a bajas velocidades y bajo condiciones críticas de contaminación por agua, jugo y bagazo, conllevando a que el aceite utilizado, no solo tenga la viscosidad correcta a la temperatura de operación, sino que también el modificador de fricción Extrema Presión EP, cuente con la capacidad de carga en la prueba de 4 bolas, ASTM D2783 de acuerdo con el torque transmitido. En estas condiciones de trabajo, el modificador de fricción forma la Capa límite antifricción 1 y la viscosidad la Capa fluida 3 de la película lubricante. Para poder determinar la capacidad de carga del modificador de fricción EP se debe calcular primero el torque transmitido en Nm, de lo contrario, si es inferior a la requerida, se presentará desgaste anormal por adhesión y por fatiga superficial, reduciendo la Vida disponible en horas de operación de las coronas de los Molinos.
2. TANDEM DE MOLINOS
El Tandem de Molinos está constituido por seis Molinos, cada uno de los cuales cuenta con un motor eléctrico, acople de piñones, un reductor de velocidad, acople de araña, tres coronas para accionamiento de la masa superior, masa cañera, masa bagacera y cuarta masa. Los Molinos de mayor torque son el 1 y el 6, se va a tomar el Molino 1 para determinar el modificador de fricción EP que se debe utilizar. Los datos técnicos de las Coronas del Molino 1, son los siguientes:
1. Torque total en el eje de entrada a la corona superior, 2´358.163 Nm.
2. Torque en el eje de la corona, 786.054 Nm.
3. Velocidad de la corona, 6 rpm.
4. Temperatura de operación, 49°C.
5. Diámetro de paso, 1230 mm.
6. Longitud del diente, 660 mm.
7. Altura de los dientes, 200 mm.
8. Número de dientes, 22.
9. Angulo de hélice, 0°.
10. Angulo de presión normal, 25°.
11. Acabado superficial ISO 468, N12.
12. Rugosidad crítica, 50 ?m.
13. Rugosidad RMS, 70,71 micra.
14. Material, acero forjado 4140.
15. Dureza 400/450 HB.
16. Vida disponible de las coronas, 25.920 horas.
17. Vida real de las coronas, 16.500 horas.
3. LUBRICACION
La lubricación de las coronas superior, cañera y bagacera es por gota – gota a plena pérdida donde el aceite que se aplica forma la película lubricante, reduce la fricción, enfría, amortigua y evacua impurezas, pero se consume de tal manera que es necesario aplicar cierta cantidad dentro de un período de tiempo determinado. Se va a verificar, para las condiciones reales de producción, la capacidad de carga en 4 bolas, ASTM D2783, del modificador de fricción Extrema Presión.
4. CALCULO DEL TORQUE DE LAS CORONAS DEL MOLINO 1
Los cálculos se pueden hacer con el Molino 1 o el 6 que son los de mayor torque; en este caso se va a tomar el Molino 1. El sistema de transmisión de potencia está constituido por un motor eléctrico, un acople 1, un reductor de velocidad de seis ejes, un acople 2, tres coronas, una masa superior, una masa cañera, una masa bagacera, y una cuarta masa. Se debe calcular el torque que recibe cada corona para poder determinar las características del lubricante a utilizar. Ver Figura 1.
Características del reductor de velocidad
1. Engranajes cilíndricos de dientes helicoidales.
2. Rodamientos de rodillos a rótula.
3. Piñón 1 con 28 dientes montado en el eje 1.
4. Engranaje 1 con 107 dientes montado en el eje 2.
5. Relación de transmisión entre el engranaje 1 y el piñón 1, 107/28 igual a 3,82.
6. Velocidad del eje 1 1.200 rpm.
7. Piñón 2 con 23 dientes montado en el eje 2.
8. Engranaje 2 con 90 dientes montado en el eje 3.
9. Relación de transmisión entre el engranaje 2 y el piñón 2, 90/23 igual a 3,91.
10. Velocidad del eje 2 de 314,13 rpm.
11. Piñón 3 con 21 dientes montado en el eje 3.
12. Engranaje 3 con 21 dientes montado en el eje 4.
13. Relación de transmisión entre el engranaje 3 y el piñón 3, 21/21 igual a 1.
14. Velocidad del eje 3 de 80,34 rpm.
15. Piñón 4 con 21 dientes montado en el eje 4.
16. Engranaje 4 con 75 dientes montado en el eje 5.
17. Relación de transmisión entre el engranaje 4 y el piñón 4, 75/21 igual a 3,57.
18. Velocidad del eje 4 de 80,34 rpm.
19. Piñón 5 con 21 dientes montado en el eje 5.
20. Engranaje 5 con 79 dientes montado en el eje 6.
21. Relación de transmisión entre el engranaje 5 y el piñón 5, 79/21 igual a 3,76.
22. Velocidad del eje 5 de 22,50 rpm.
23. Velocidad del eje 6 de 6 rpm.
24. Relación total de transmisión de 200.
Nota: El piñón 3 y el engranaje 3 tienen el mismo número de dientes, por lo tanto, el torque en el eje 3 y en el eje 4 es el mismo. Este es un diseño muy particular del fabricante de este reductor de velocidad. Ver Figura 2.
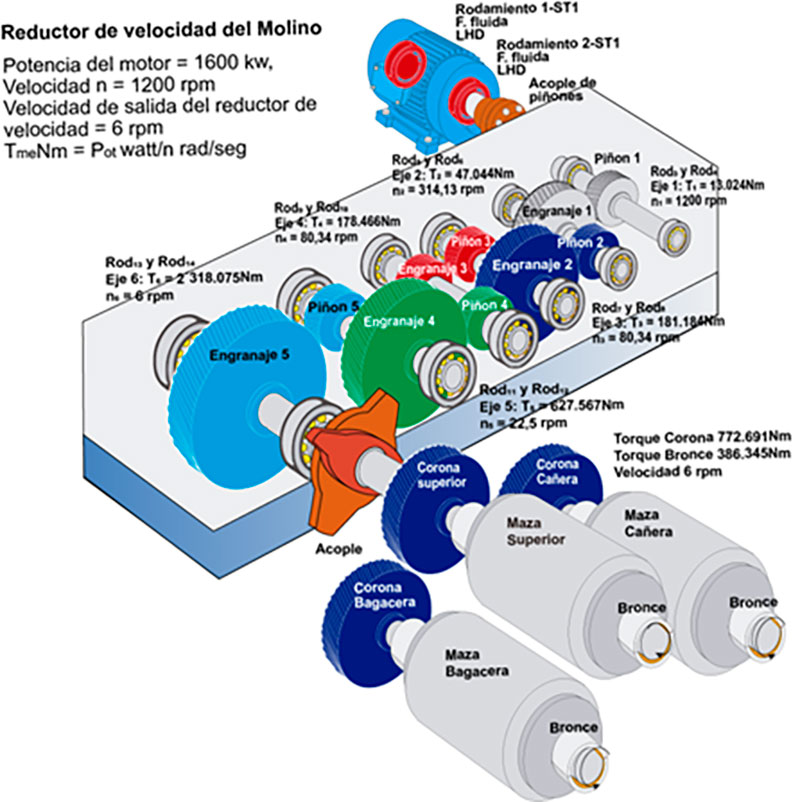
FIGURA 2 | Sistema de transmisión del Molino 1
Cálculo del Torque en la corona superior, cañera y bagacera
El torque disponible en la corona superior, en la corona cañera y en la corona bagacera se calcula a partir del torque en Nm entregado por el motor eléctrico al reductor de velocidad el cual lo multiplica 200 veces y se lo transmite a la corona de la masa superior la cual lo distribuye con las otras dos coronas. El torque TmeNm generado por el motor eléctrico se calcula de:
TmeNm = Pot watt/n, rad/seg Ecuación 1
Donde:
1. Tme: Torque generado por el motor eléctrico en Newtonxmetro (Nm).
2. Pot: Potencia del motor eléctrico en watt.
3. n: velocidad angular del eje del motor eléctrico en rad/seg.
Por lo tanto, se tiene que el torque TmeNm generado por el motor eléctrico es de:
Pot watt = 1600 kw = 1’600.000 watt; n = 1200revol/minx2x3,1416rad/revolx1min/60seg = 125,66 rad/seg.
TmeNm = 1´600.000watt/125,66rad/seg = 12.732Nm.
El rodamiento 1 y 2 son rígidos de bolas, aceite sintético, velocidad del eje del motor eléctrico 1200 rpm, fricción fluida, LHD, aceite de grado ISO 100 AW. El torque disponible en el eje del motor eléctrico Tme eje Nm es igual a:
Tme eje Nm = 12.732Nm – [(ffrod1 + ffrod2)/2 + fsac]x12.732Nm – [(0,001 + 0,001)/2 + 0,012]x12.732Nm = 12.732Nm – 165,51Nm = 12.566 Nm.
ffrod1 y ffrod2 es el coeficiente de fricción fluida en el rodamiento 1 y 2 y fsac es el coeficiente de fricción sólida en el acople de piñones.
Tme eje en el eje del motor eléctrico = 12.566 Nm.
Torque en el eje 1
El rodamiento 3 y 4 son de rodillos a rótula, aceite sintético, velocidad en el eje 1 de 1200 rpm. En los rodamientos la fricción es fluida, LHD, aceite de grado ISO 100 AW.
Torque en el eje 1 = 12.566Nm – [(ffrod3 + ffrod4)/2 + 2xfeca]x12.566Nm = 12.566Nm – [(0,003 + 0,003)/2 + 2×0,001]x12.566Nm = 12.566 Nm – 62,83Nm = 12.503Nm.
frod3, frod4 es el coeficiente de fricción fluida en el rodamiento 3 y 4 y feca es el coeficiente de fricción equivalente por circulación de aceite al rodamiento 3 y 4.
Torque neto en el eje 1 = 12.503Nm
Torque en el eje 2
Piñón 1 con 28 dientes y engranaje 1 con 107 dientes. La relación de transmisión, rt entre el engranaje 1 y el piñón 1 es de 107/28 y es igual a 3,82.
Torque en el eje 2 = 3,82×12.503Nm = 47.761Nm; velocidad del eje 2 = 1.200rpm/3,82 = 314,13 rpm.
El rodamiento 5 y el 6 son de rodillos a rótula, aceite sintético, velocidad de 314,13 rpm. En los rodamientos y en el punto de engrane la fricción es mixta permanente, LEHD, aceite de grado ISO 220 EP1.
Torque neto en el eje 2 = 47.761Nm – [(fmrod5 + fmrod6)/2 + fmp1-e1 + fesae1 + 3xfeca]x47.761Nm.
Torque neto en el eje 2 = 47.761Nm – [(0,003 + 0,003)/2 + 0,007 + 0,002 + 3×0,001]x47.761Nm =
47.761Nm – 716,41Nm = 47.044Nm.
fmrod5, fmrod6 es el coeficiente de fricción mixta permanente en el rodamiento 5 y 6, fmp1-e1 es coeficiente de fricción mixta permanente en el punto de engrane entre el engranaje 1 con el piñón 1, fesae1 es el coeficiente de fricción equivalente por el salpique de aceite del engranaje 1 y feca es el coeficiente de fricción equivalente por circulación de aceite a los rodamientos y punto de engrane.
Torque neto en el eje 2 = 47.044Nm
Torque en el eje 3
Piñón 2 con 23 dientes y engranaje 2 con 90 dientes. La relación de transmisión, rt entre el engranaje 2 y el piñón 2 es de 90/23 y es igual a 3,91.
Torque en el eje 3 = 3,91×47.044Nm = 183.944 Nm.
Velocidad en el eje 3 = 314,13rpm/3,91 = 80,34 rpm.
El rodamiento 7 y el 8 son de rodillos a rótula, aceite sintético, velocidad 80,34 rpm. En los rodamientos y en el punto de engrane, la fricción es mixta permanente, LEHD, aceite de grado ISO 320 EP2.
Torque neto en el eje 3 = 183.944 Nm – [(fmrod7 + fmrod8)/2 + fmp2-e2 + fesae2 + 3xfeca]x183.944 Nm
Torque neto en el eje 3 = 183.944 Nm – [(0,003 + 0,003)/2 + 0,007 + + 0,002 + 3×0,001)]x183.944 Nm = 183.944 Nm – 2.759Nm = 181.184Nm.
fmrod7, fmrod8 es el coeficiente de fricción mixta permanente en el rodamiento 7 y 8, fmp2-e2 es coeficiente de fricción mixta permanente en el punto de engrane entre el engranaje 2 con el piñón 2, fesae2 es el coeficiente de fricción equivalente por el salpique de aceite del engranaje 2 y feca es el coeficiente de fricción equivalente por circulación de aceite a los rodamientos y punto de engrane.
Torque neto en el eje 3 = 181.184Nm.
Torque en el eje 4
Piñón 3 con 23 dientes y engranaje 3 con 23 dientes. La relación de transmisión, rt entre el engranaje 3 y el piñón 3 es de 23/23 y es igual a 1.
Torque en el eje 4 = 1×181.184Nm = 181.184 Nm.
Velocidad en el eje 4 = 80,34/1 = 80,34 rpm.
El rodamiento 9 y 10 son de rodillos a rótula, aceite sintético, velocidad 80,34 rpm. En los rodamientos y en el punto de engrane, la fricción es mixta permanente, LEHD, aceite de grado ISO 320 EP2.
Torque neto en el eje 4 = 181.184 Nm – [(fmrod9 + fmrod10)/2 + fmp3-e3 + 3xfeca]x181.184 Nm
Torque neto en el eje 3 = 181.184 Nm – [(0,003 + 0,003)/2 + 0,007 + 3×0,001]x181.184 Nm = 181.184 Nm – 2.717Nm = 181.184Nm.
fmrod9, fmrod10 es el coeficiente de fricción mixta permanente en el rodamiento 7 y 8, fmp3-e3 es coeficiente de fricción mixta permanente en el punto de engrane entre el engranaje 3 con el piñón 3 y feca es el coeficiente de fricción equivalente por circulación de aceite a los rodamientos y punto de engrane.
Torque neto en el eje 4 = 178.466Nm.
Torque en el eje 5
Piñón 4 con 21 dientes y engranaje 4 con 75 dientes. La relación de transmisión, rt entre el engranaje 4 y el piñón 4 es de 75/21 y es a 3,57.
Torque en el eje 5 = 3,57×178.466Nm = 637.124Nm.
Velocidad en el eje 5 = 80,34rpm/3,57 = 22,5 rpm.
El rodamiento 11 y el 12 son de rodillos a rótula, aceite sintético, velocidad 22,5 rpm. En los rodamientos y en el punto de engrane la fricción es mixta permanente, LEHD, aceite de grado ISO 680 EP3.
Torque neto en el eje 5 = 637.124Nm – [(fmrod11 + fmrod12)/2 + fmp4-e4 + fesae4 + 3xfeca]x637.124Nm.
Torque neto en el eje 5 = 637.124Nm – [(0,003 + 0,003)/2 + 0,007 + 0,002 + 3×0,001]x637.124Nm = 637.124Nm – 9.556Nm = 627.567Nm.
fmrod11, fmrod12 es el coeficiente de fricción mixta permanente en el rodamiento 11 y 12, fmp4-e4 es coeficiente de fricción mixta permanente en el punto de engrane entre el engranaje 4 con el piñón 4, fesae4 es el coeficiente de fricción equivalente por el salpique de aceite del engranaje 4 y feca es el coeficiente de fricción equivalente por circulación de aceite a los rodamientos y punto de engrane.
Torque neto en el eje 5 = 627.567 Nm.
Torque en el eje 6 o de salida
Piñón 5 con 21 dientes y el engranaje 5 con 79 dientes. La relación de transmisión, rt entre el engranaje 5 y el piñón 5 es de 79/21 igual a 3,75.
Torque en el eje 6 = 3,75×627.567Nm = 2´353.376Nm.
Velocidad en el eje 6 = 22,5rpm/3,75 = 6 rpm.
El rodamiento 13 y 14 son de rodillos a rótula, aceite sintético, velocidad 6 rpm, En los rodamientos y en el punto de engrane la fricción es mixta permanente, LEHD, aceite de grado ISO 3200 EP4.
Torque neto en el eje 6 = 2´353.376Nm – [(fmrod13 + fmrod14)/2 + fmp5-e5 + fesae5 + 3xfeca]x2´353.376Nm.
Torque neto en el eje 6 = 2´353.376Nm – [(0,003 + 0,003)/2 + 0,007 + 0,002 + 3×0,001]x2´353.376Nm = 2´353.376Nm – 35.300Nm = 2´318.075Nm.
fmrod11, fmrod12 es el coeficiente de fricción mixta permanente en el rodamiento 11 y 12, fmp5-e5 es coeficiente de fricción mixta permanente en el punto de engrane entre el engranaje 5 con el piñón 5, fesae5 es el coeficiente de fricción equivalente por el salpique de aceite del engranaje 5 y feca es el coeficiente de fricción equivalente por circulación de aceite a los rodamientos y punto de engrane.
Torque neto en el eje 6 = 2´318.075 Nm.
Torque en la corona superior, cañera y bagacera:
Son tres coronas:
Torque en el eje de cada corona = 2’318.075Nm/3 = 772.691Nm
Torque en el bronce de apoyo de cada masa:
Son seis bronces, dos por cada masa:
Torque en cada bronce de las masas = 772.691Nm/2 = 386.345Nm
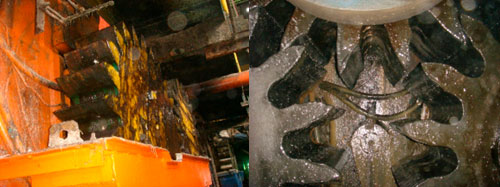
FIGURA 3 | Corona superior, cañera y bagacera del Molino 1
5. CAPACIDAD DE CARGA DEL MODIFICADOR DE FRICCION EXTREMA PRESION EN FUNCION DEL TORQUE EN Nm
1. Extrema Presión EP1: Grupo 1 o 1ra generación a base de fósforo y azufre, para Torques desde 5.000 Nm hasta de 100.000 Nm, con una capacidad de carga en la prueba de 4 bolas ASTM D2783/ASTM D2592, de 150 kgf hasta 350 kgf.
2. Extrema Presión EP2: Grupo 2 o 2da generación a base de grafito, bisulfuro de molibdeno (MoS2), Teflón, PTFE (Politetrafluoroetileno), para torques mayores de 100.000 Nm hasta 500.000 Nm con una capacidad de carga en la prueba de 4 bolas ASTM D2783/ASTM D2592, mayor de 350 hasta 750 kgf.
3. Extrema Presión EP3: Grupo 3 o 3ra generación a base de boratos, tungsteno, para torques mayores de 500.000 Nm hasta 1´000.000 Nm, con una capacidad de carga en la prueba de 4 bolas ASTM D2783/ASTM D2592, mayor de 750 kgf hasta 1350 kgf.
4. Extrema Presión EP4: Grupo 4 o 4ra generación a base de bisulfuro de tungsteno, para torques mayores de 1´000.000 Nm hasta 3´000.000 Nm, con una capacidad de carga en la prueba de 4 bolas ASTM D2783/ASTM D2592 mayor de 1350 kgf hasta 2500 kgf.
Carga a la soldadura y prueba de desgaste del modificador de fricción Extrema Presión en la prueba de 4 bolas ASTM D2783
La carga a la soldadura y la prueba de desgaste de los modificadores de fricción Extrema Presión se especifica en la Tabla 2.
No | Generación del modificador de fricción EP | Carga a la soldadura kgf | Prueba de desgaste, huella mm |
---|---|---|---|
01 | Antidesgaste | Desde 28 hasta 150 | Hasta 2 |
02 | 1ra generación | Desde 150 hasta 350 | Hasta 1 |
03 | 2da generación | Desde 350 hasta 750 | Hasta 0,9 |
04 | 3ra, 4ta generación | Desde 750 hasta 1350 | Hasta 0,8 |
Para un torque en la corona superior, cañera y bagacera de 772.691Nm, se tiene que se requiere que el lubricante tenga modificadores de fricción Extrema Presión de tercera generación (torque entre 500.000 Nm y 1´000.000Nm) con una capacidad de carga en la prueba de 4 bolas ASTM D2783 entre 750 kgf y 1350 kgf. Interpolando se tiene que, para un torque de 772.691 Nm, la capacidad de carga debe ser de 1017,22 Kgf. El porcentaje de incremento en la capacidad de carga con respecto a la mínima de 750 kgf es de 44,53%. La condición de fricción en los dientes de las coronas es mixta permanente y la condición de lubricación es Elastohidrodinámica (EHD).
De la Tabla 3 se selecciona, con base en el modificador de fricción Extrema Presión EP3 de tercera generación, el factor de seguridad de la película lubricante (?) que para engranajes está entre 0,1 y 0,05. Teniendo en cuenta que el porcentaje de incremento en la capacidad de carga con respecto a la mínima de 750 kgf debe ser del 44,53%, se tiene que, en esta misma proporción, se afecta el factor de seguridad de la película lubricante (?) y por lo tanto queda en 0,077.
No | Mecanismo | Modificador de fricción Extrema Presión EP | ||||
---|---|---|---|---|---|---|
Valor de lambda | ||||||
Antidesgaste | 1ra generación | 2da generación | 3ra, 4ta generación | Lubricación hidrostática | ||
01 | Rodamientos | 1,0 <= lambda <= 2,5 | 0,5 <= lambda <= 1,0 | 0,1 <= lambda <0,5 | 0,05 <= lambda < 0,1 | No aplica |
02 | Cojinetes lisos | 1,0 <= lambda <= 2,0 | 0,5 <= lambda <= 1,0 | 0,1 <= lambda <0,5 | 0,05 <= lambda < 0,1 | lambda < 0,05 |
03 | Engranajes | 1,0 <= lambda <= 1,5 | 0,5 <= lambda <= 1,0 | 0,1 <= lambda <0,5 | 0,05 <= lambda < 0,1 | No aplica |
6. CONCLUSIONES
– Al calcular el torque en Nm entre los ejes del reductor de velocidad es necesario tener en cuenta las pérdidas por fricción en los mecanismos asociados a cada eje como son los rodamientos y engranajes.
– Las pérdidas por fricción dependen del tipo de fricción, si es sólida, mixta o fluida.
– Para torques inferiores a 5.000 Nm la fricción en ,los rodamientos y engranajes por lo regular es fluida y la lubricación es hidrodinámica y para valores superiores la fricción es mixta y la lubricación es Elastohidrodinámica y el tipo de modificador de fricción Extrema Presión que debe tener el aceite depende del torque transmitido.
– Una vez determinado cuál el modificador de fricción EP que debe tener el aceite, se halla su capacidad de carga en kgf en la prueba de desgaste de 4 bolas, ASTM D2783, interpolando entre los valores mínimo y máximo del torque y la capacidad de carga del EP seleccionado teniendo en cuenta el valor del torque de trabajo.
– Si el modificador de fricción EP para el aceite que lubrica las coronas de los Molinos de los Ingenios Azucareros no se selecciona correctamente de acuerdo con el torque de trabajo, se tendrán problemas de desgaste anormal o fallas por adhesión o por fatiga superficial a corto o a mediano plazo en los dientes de las coronas, incrementando considerablemente los costos de mantenimiento.